24 Dec What Are CNC Waterjet Repairs Costing You?
What Are CNC Waterjet Repairs Costing You?
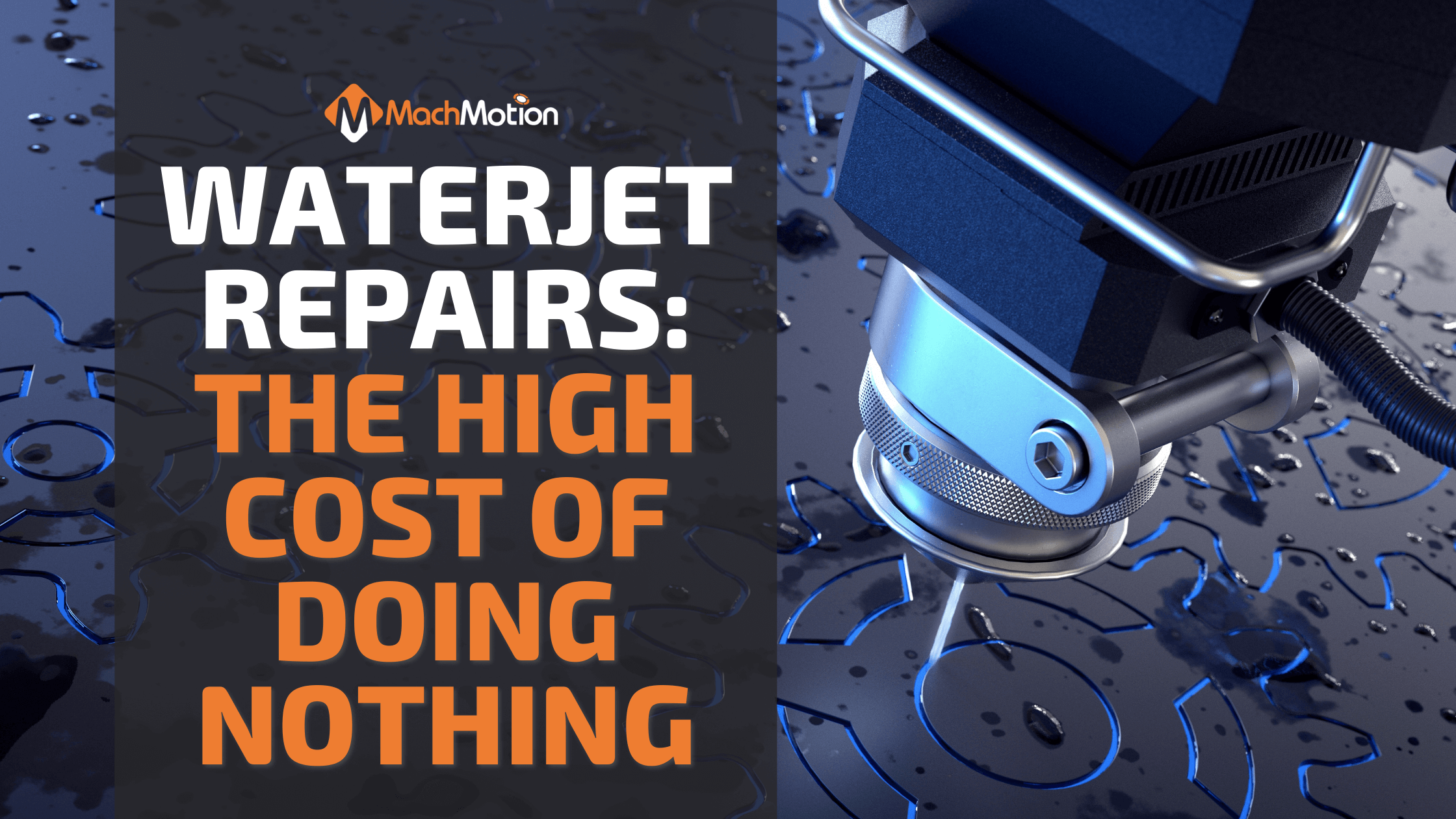
The High Cost Of Doing Nothing
It’s no secret, CNC waterjet repairs can be extremely costly to your business. Oftentimes, we find shop machines have been repaired just enough to keep them going a little bit longer. It’s not long before they are experiencing another breakdown. When the time comes to make CNC repairs or buy replacement parts, that original short-term fix to keep production going could leave you with a hefty long-term bill or even worse, an unusable waterjet. A CNC waterjet repair that may appear to be cost-effective in the short term could lead to bigger problems in the future. The key here is to consider the long-term consequences of a quick repair decision. We’re going to take a look at some of the costs of CNC waterjet repairs including unexpected downtime, sourcing obsolete parts, employee morale, and customer trust. What could these be costing your company? Read on to find out.
Recurring Unscheduled Downtime
If you begin encountering delays in cutting time, errors during operation, or just general unreliability in your CNC waterjet, downtime becomes an annoying and common occurrence on the shop floor. When downtime begins to become normal, instead of the exception, your team can begin to suffer costly effects on production. In repairs, downtime costs money that you could be spending on other projects or adding to your bottom line. Fortunately, there are long-lasting solutions that can save you time & money by giving your waterjet a second lease on life. Keep reading to see how you can protect your investment!
Obsolete or Hard To Find Replacement Parts
Sourcing replacement parts for a new machine may not be an issue, but what happens when you’re dealing with an older waterjet, no longer supported by the OEM? Many business and manufacturing facilities find themselves with legacy machinery and equipment. While the occasional breakdown won’t ruin your busy season, repeated lengthy CNC waterjet repairs can cost you plenty if it occurs too often. These breakdowns are also very frustrating for your staff to deal with. Servicing your machines regularly helps keep your waterjet running for longer. Once you begin experiencing controller issues or run into other problems, you could be looking at long lead times for replacement waterjet parts. You may even find yourself in a worse situation than you had anticipated at the start. Considering a long-term solution upfront can save you headaches down the road.
Low Workplace Morale
Whether you’re a manager or a team member, losing productivity is easily one of the biggest reasons for low morale. An organization’s morale is crucial to longstanding success. On many occasions, this loss of productivity can be caused by machine breakdowns & controller issues. Low morale can also be caused by failing to address long-term solutions for CNC waterjet repair issues in your company ahead of time. By staying ahead of your machine you can put your best foot forward to serve your customers and your team with the tools they need to succeed. If something is not working, there’s no reason to let the issue continue to go unaddressed, right?
Trust Declines Among Customers
When you’re running a busy operation, if your waterjet isn’t reliable and goes down unexpectedly, you can begin losing your customers’ trust. They know that there is always a risk that their project may be delayed due to unforeseen problems caused by the equipment, but it can cause harm to your bottom line if it begins to happen regularly. Customers may have a hard time trusting your business with future orders after experiencing one too many delays. That’s a big problem! You don’t want to lose customers because your waterjet isn’t dependable.
What Can I Do To Protect My Investment?
Be proactive! Don’t wait until your machine breaks down to solve problem after problem with short-term fixes. A well-planned control retrofit is a long-term solution that can help mitigate the high cost of unexpected CNC waterjet failures. One great benefit is being able to schedule your downtime during a slower period, not to disrupt your busy season. Keeping your waterjet machines in your shop that you’re already familiar with and have fixturing & tooling to support also helps keep costs lower.
Although retrofitting is not an alternative to preventative maintenance, it is a solid solution to eliminate expensive unexpected downtime and extend the lifespan of your CNC Waterjet. With a cost-effective CNC Waterjet Retrofit solution from MachMotion, you’ll get the service of a high-end cutting machine, without the price tag of buying a new” one. Click here to see a short video on what the MachMotion experience can offer your company’s equipment.
We retrofit all different brands of CNC Waterjets including Flow, Biesse, OMAX, KMT Waterjets, AIM MasterJetSaw, and many more popular waterjet brands! Learn more about planning a CNC Waterjet Retrofit by visiting this link or by filling out the form below to get in touch with one of our experienced retrofit experts today!