26 Jan Understanding CNC Control Lifecycles With MachMotion
Understanding CNC Control Lifecycles With MachMotion
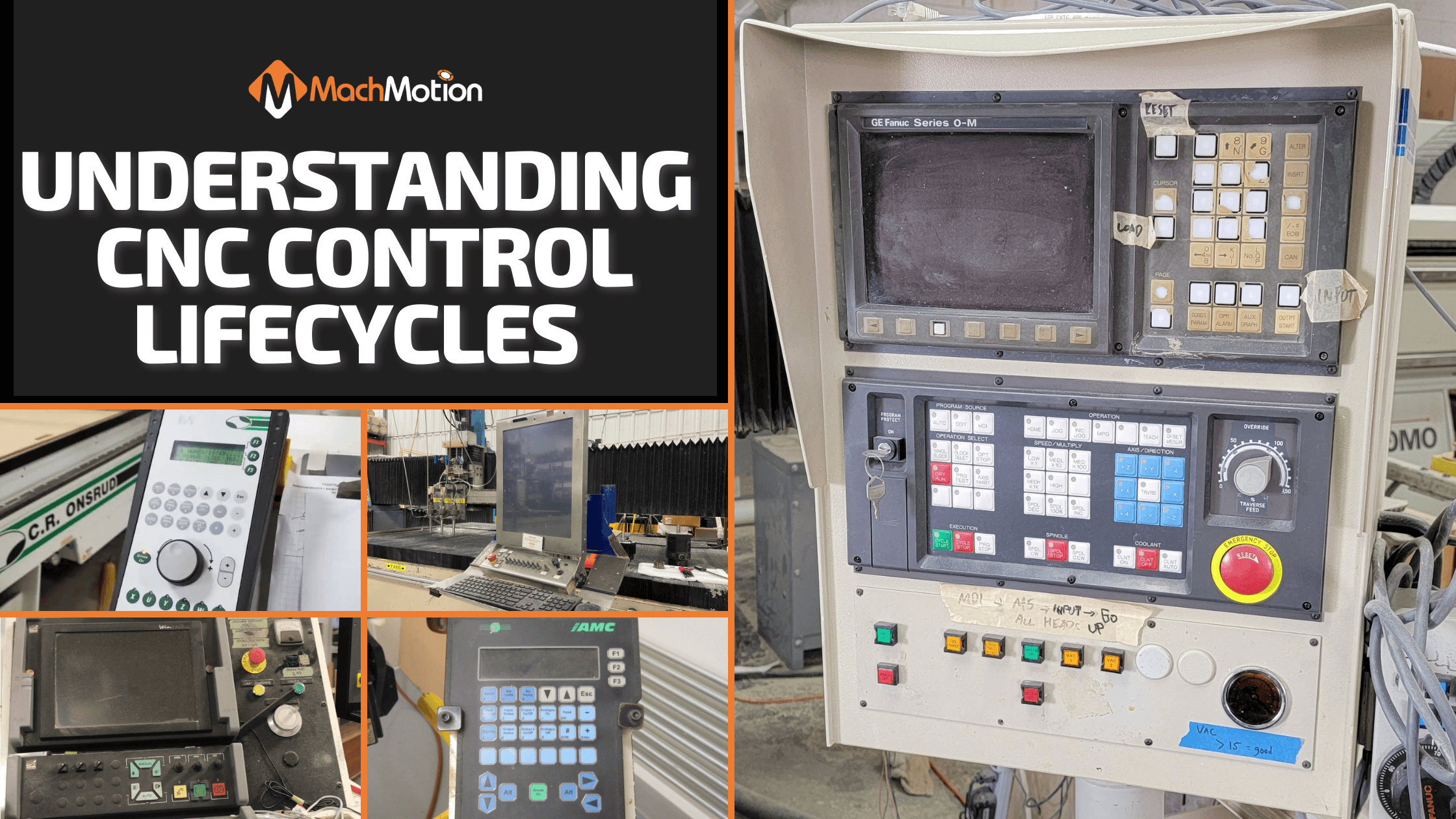
Manufacturing is constantly evolving and advancing technologies, playing a major role in industry evolution. With those advancements comes obsolescence of technology, such as CNC controls. Though the CNC machine frames were built to last the test of time, the same cannot be said for their controls.
The lifecycle of these controls takes center stage in defining the efficiency, precision, and adaptability of the entire CNC machine. In an era of fast technological acceleration, understanding this lifecycle becomes crucial for success for CNC owners and operators. Continue reading to take a closer look at what CNC control lifecycles looks like and how you can protect your investments.
The Lifecycle Starts With When You Bought Your Machine
The journey of the CNC control lifecycle begins with the introduction of a new control integrated into your CNC machine. At this initial stage, technology is at its peak, defining new standards for efficiency and precision within the realm of CNC machines. In their prime, these controllers operate CNC machines with optimal efficiency and unparalleled precision at that time. When your controllers are at their peak, they operate CNC machines efficiently with precision. As years pass, this narrative changes.
Problems In System Operations As A Result Of Aging
As the CNC Control lifecycle continues, what was once considered cutting-edge gradually matures becoming less reliable and more challenging to operate. After years of use, your CNC control system passively communicates signs that indicate your CNC control system is aging. When the control starts becoming slow to startup and glitches disrupt your operation, these are key indicators of an aging control system.
Slow startups translate to precious minutes lost in production and glitches introduce uncertainties in the precision of your operations. A dated controller interface can feel like a relic from a bygone era and make it difficult to onboard new operators. Network security problems can also pose a threat to your confidential data as controls age and are no longer updated. Problems with the control aren’t the only hindrance, as OEM no longer supports or the manufacturer has gone out of business, leaving you without support. It’s not just about the wear and tear; it’s about maintaining a rhythm that keeps your production running smoothly.
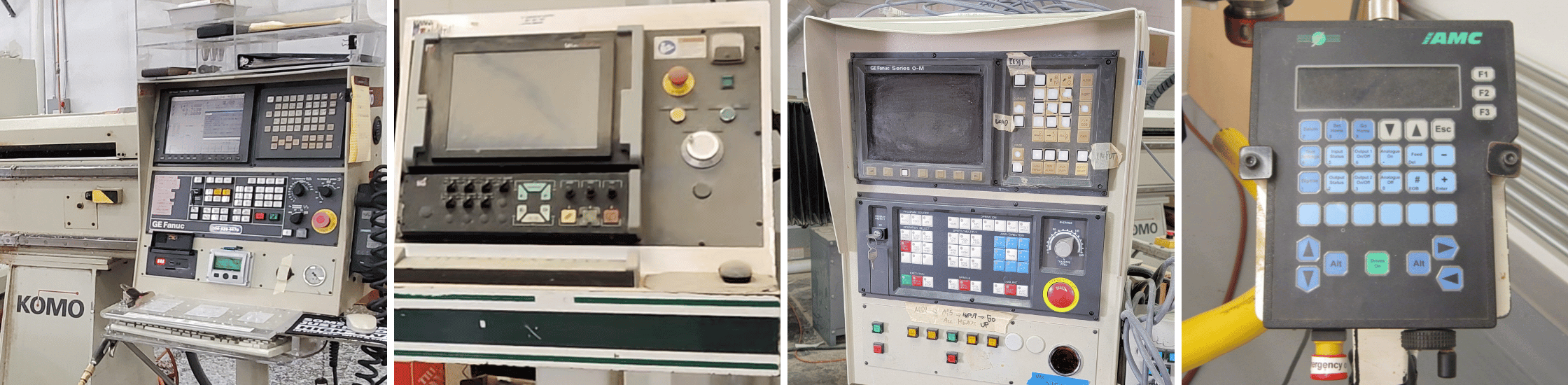
There are several signs to look for when examining aging CNC machine components:
Control System:
Evaluate existing controller performance and be cautious of glitches, slow startups, and outdated interfaces.
Software:
Check for operating systems like Windows 7, XP, NT, or a system you’ve never heard of. Obsolete systems lack support and are vulnerable to network security breaches.
Servo Systems:
Watch out for signs of wear including inconsistent cuts, abnormal movement, or vibrations.
Electrical Wiring and Components:
Examine wiring for temporary fixes and aging. Damaged wiring leads to connectivity issues. Your wires are constantly moving in a cable chain and can break or have faults over time.
Controller Obsolescence and Evolving Technology
When the CNC control lifecycle starts reaching its end, your once cutting-edge control system is now unsupported and struggles to keep up with the demands of modern manufacturing. As technology evolves rapidly, it threatens operations, customer deadlines, and profitability overall. Failure to keep up with modern advancements can mean long term problems and a dark future for your operations.
Instead of being valuable assets, these old CNC controls become obstacles in the race to become more productive and competitive. Outdated controls can lead to a domino effect of increased downtime, decreased accuracy, and rising maintenance costs among many other issues. As these problems arise they ultimately lead to much larger problems that result in lost revenue, decreased employee morale, missed deadlines, and unhappy customers.
Overcoming Obsolescence Proactively With Control Upgrades
So how can you overcome the ending of the CNC control lifecycle and position your manufacturing processes for success? CNC control upgrades can be a strategic game-changer to keep the machines you have with new, fully supported controls.
By upgrading your CNC controls with MachMotion, you not only address these pressing issues, but also propel your operations forward. Our solutions offer enhanced functionality, intuitive interfaces, robust security features, and fully-supported controls, eliminating the vulnerabilities associated with outdated systems. From enabling smoother onboarding for new operators to ensuring seamless production, a CNC control upgrade is the strategic move that empowers your existing machinery with the latest technology, enabling optimal performance and longevity. Don’t let obsolescence hold you back; embrace the power of simple, modern control systems with MachMotion.
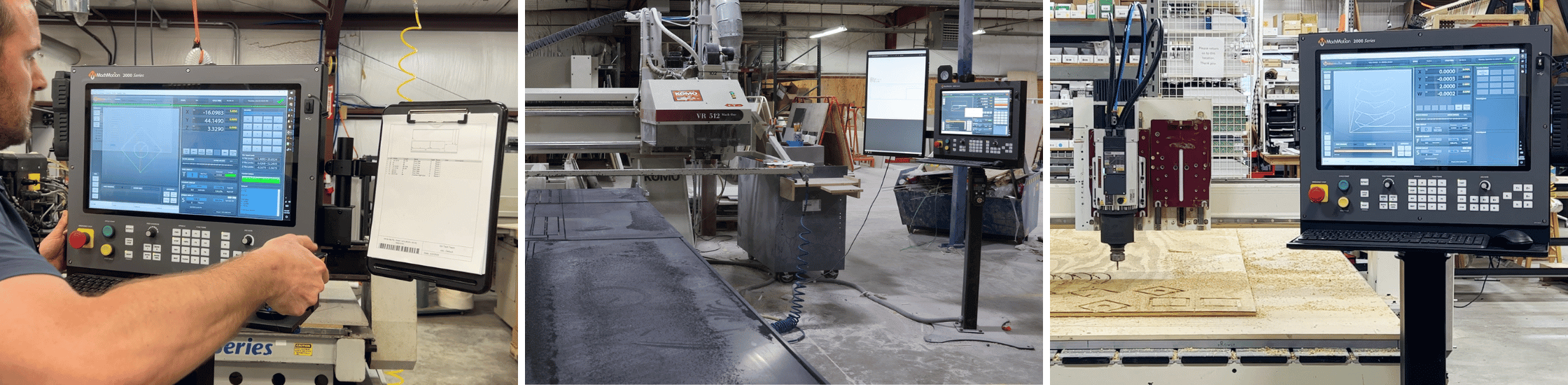
MachMotion Controller Upgrades Include:
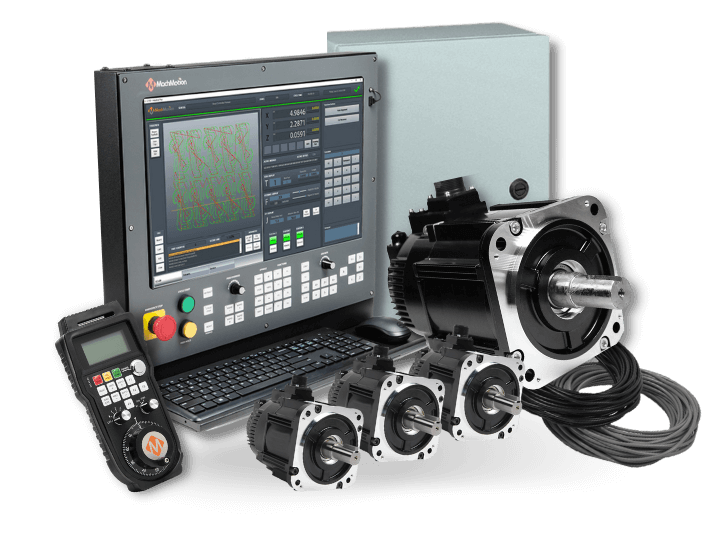
21″ Touch-screen CNC controller
Wireless pendant
Pre-wired & labeled electrical panel
Yaskawa servo drives & motors
Control mounting & stand options
1-Year Warranty
Lifetime Support
If you enjoyed reading this, be sure to check out our other articles like CNC Controls – If It’s Broke, Don’t Fix It Watch our YouTube channel for more information, tips, and customer success stories to learn more about CNC retrofits!