17 Nov TREE JOURNEYMAN 425: INSTALL STORY FROM A MACHMOTION NEWBIE
TREE JOURNEYMAN 425: INSTALL STORY FROM A MACHMOTION NEWBIE
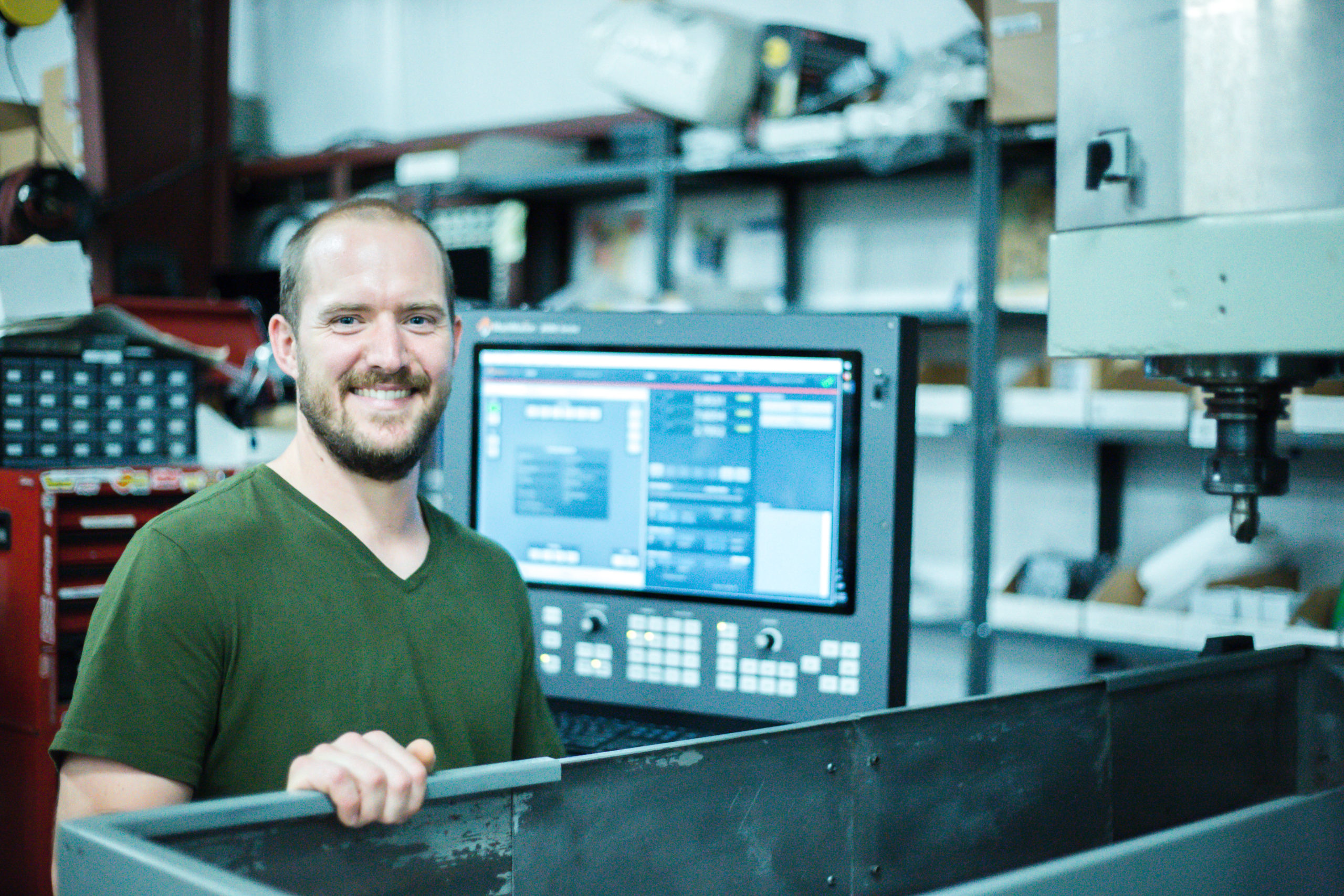
We wanted to share the experience of one of our newest team members retrofitting a CNC machine for the first time. Read about his insight into the retrofit process.
My name is Nate and I’ve been working at MachMotion for just over a month. My ONLY experience with CNC machining was as a janitor at a small machine shop when I was 15-16 years old. And, my professional background as a pastor, contractor, musician and audio/video technician make me a true jack of all trades and master of none!
I am in training to work in the Technical Support department at MachMotion. As part of my training and introduction to CNC machining, I was given the task of retrofitting a 3-axis CNC Tree Journeyman 425 knee mill using our standard 2050M knee mill kit.
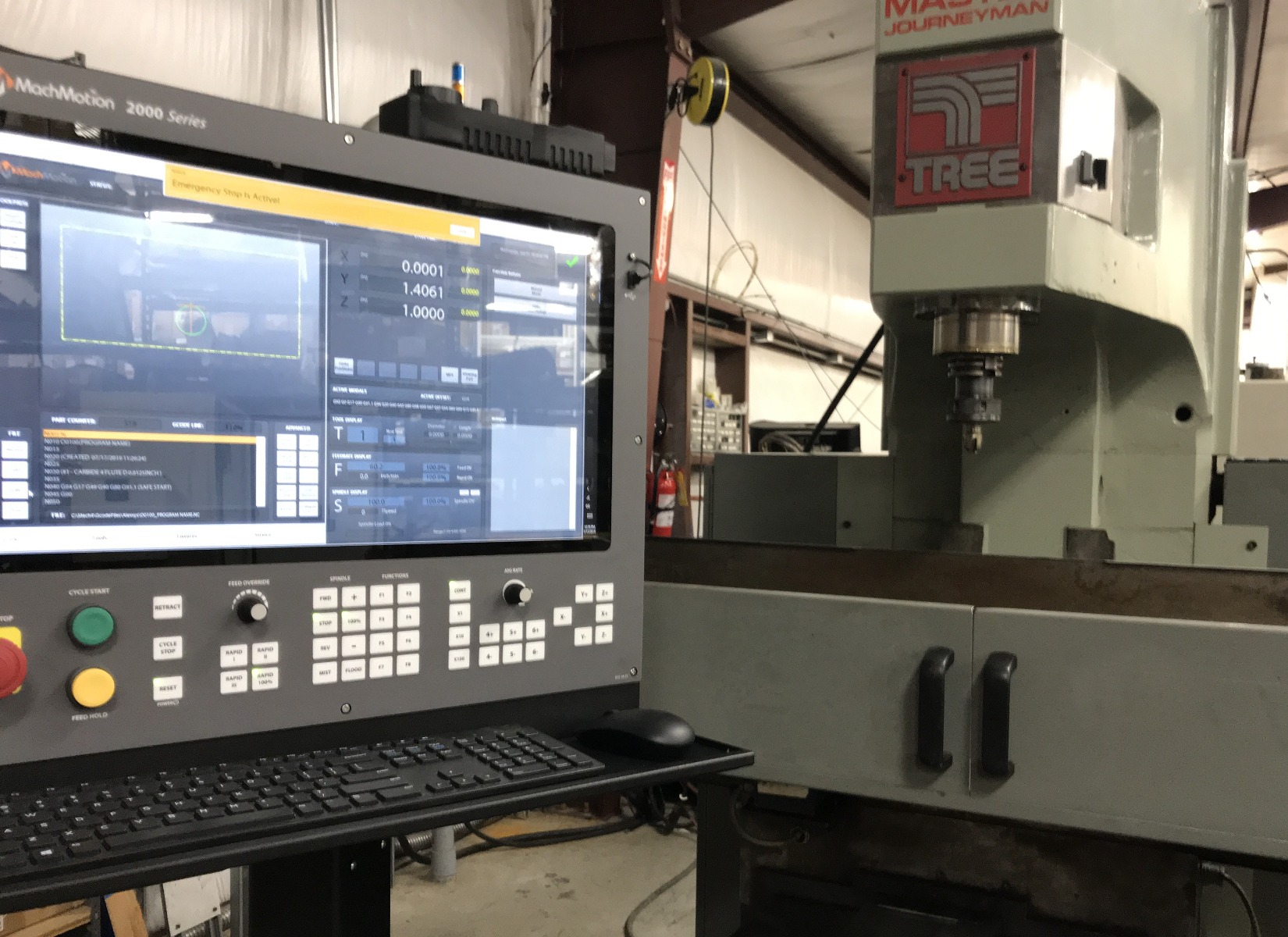
Let me just be honest and say that these machines are more complicated than anything I’ve ever worked with. The number of components that have to flawlessly work together is staggering. Virtually everything has to be configured, programmed and tuned to perfection for the machine to work.
But, two things became very apparent to me during the retrofit:
1. The team here at MachMotion has gone to painstaking efforts to build the retrofit kits in a way that makes them feel very uncomplicated. At first glance, I saw something terribly complex, but as I walked through the process it was very, very intuitive. I was able to do almost half of the install without even opening the installation manual (which I don’t recommend!) and when I did need the manual, it was a good guide on what I needed to do next. It was apparent at every turn that these systems are not just thrown together, they are designed with the user in mind.
2. When I did get in a pinch, I was never alone! Everything at MachMotion is a team effort and it’s apparent that technical support is everyone’s job. The entire team is very knowledgeable in their area of expertise and I never had to wait long before someone was readily available to point me in the right direction with clear and decisive instruction. Even when I encountered more difficult issues, there is an attitude of “improvise, adapt and overcome” that is a part of the core of this company. I never once felt like I had stalled out or was by myself.
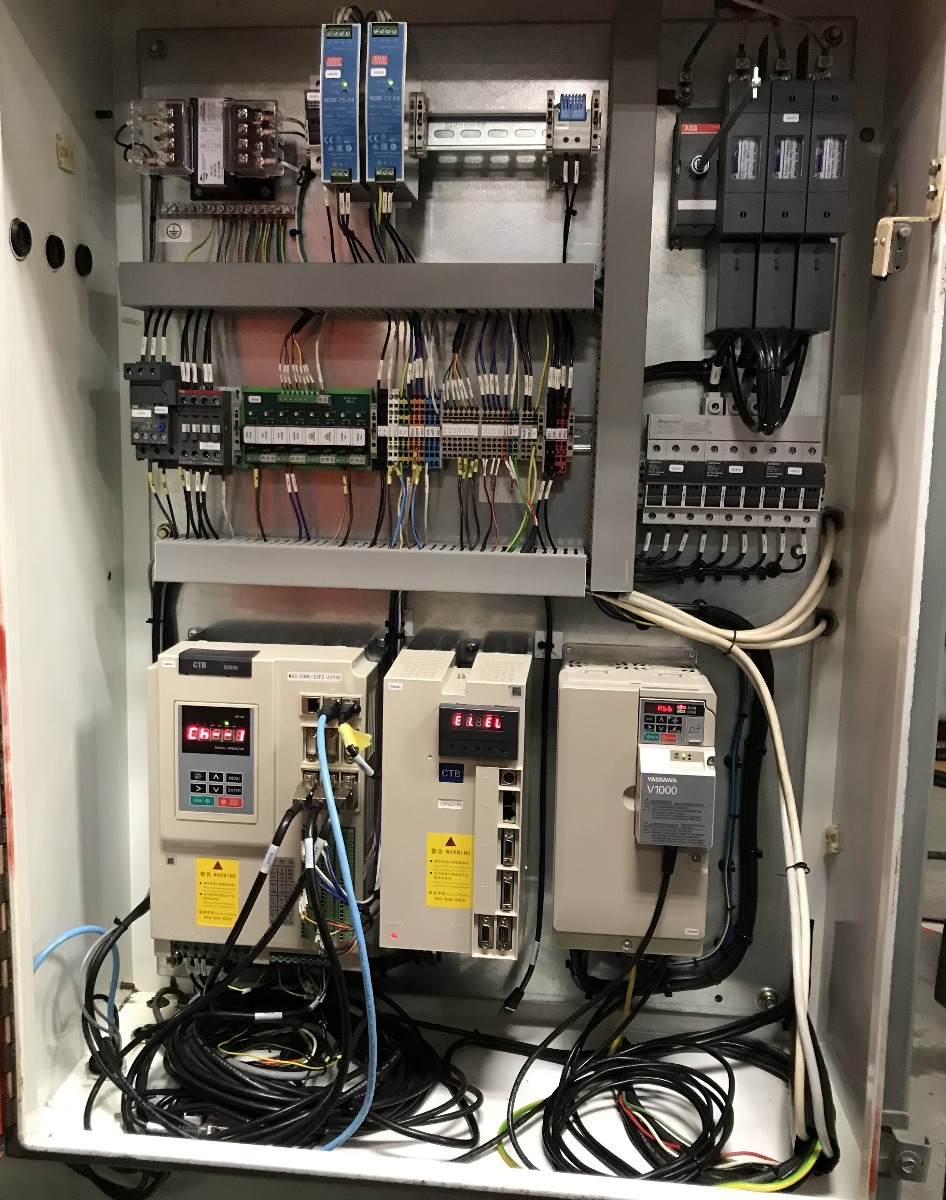
So, after two weeks, the cabinet was wired, the control was powered on, and the motors were calibrated and ready to cut parts. It was incredible to see a 30-year-old system that could easily have been sent to the scrap heap find a second life as a functional CNC machine.