02 May Top 5 Problems With Obsolete CNC Controls
Top 5 Problems With Obsolete CNC Controls
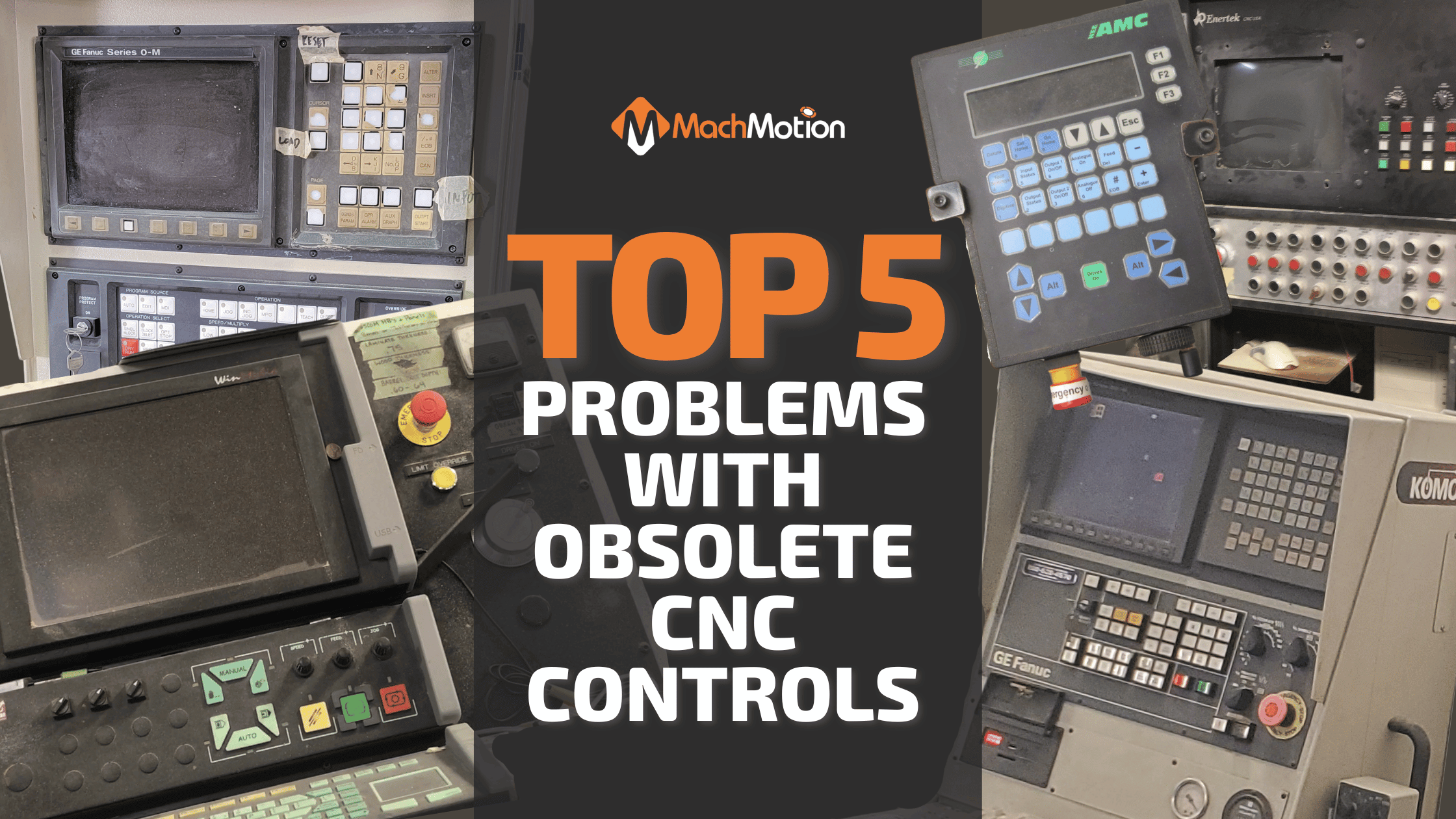
Are you all too familiar with obsolete CNC controls? Imagine using a personal computer from 5 years ago, 10 years ago, 15 or 20 years ago. Can you imagine how much your productivity would come to a halt? Is your CNC suffering from less effective, less efficient, and unreliable controls?
With technology advancing rapidly, older CNC machines with obsolete CNC controls are becoming less effective, less efficient, and unreliable. This leads to a significant decline in productivity and revenue for many manufacturing companies. Causing a variety of problems that range from frequent unplanned downtime to difficulty training new operators, obsolete CNC controls have become a burdensome obstruction to many production processes. In this blog, we will explore the top 5 most common problems that CNC owners experience with obsolete controllers and how a CNC retrofit can solve them.
Top 5 Problems With Obsolete CNC Controls:
-
- Sudden Downtime and Unplanned Maintenance
- Limited Capabilities
- Difficulties in Obtaining Spare Parts
- Inefficiency and Inaccuracy
- Challenges in Training New Operators
Problem #1: Sudden Downtime and Unplanned Maintenance
There’s no shame in operating an older CNC machine, but one of the biggest problems with obsolete CNC controls is the high rate of downtime and unplanned maintenance. When the control suddenly starts flickering or the machine has to be powered on at all times just to keep it running, you end up spending more time and energy keeping it alive than focusing on production. As older controls become more outdated, they become more prone to malfunctions and failure, leading to unplanned downtime and maintenance issues. This oftentimes results in companies missing customer deadlines, lost profits, and damaging employee morale.
Problem #2: Limited Capabilities
Another problem with obsolete CNC controls is limited capabilities. Are you keeping up with your competitors in a way that will keep your company moving forward in the future? As technology advances, older controls become less and less capable of keeping up with modern production demands.The rise of automation and Industry 4.0 concepts in manufacturing has led to increased demand for CNC machines that can seamlessly integrate with automated systems, data exchange, and real-time monitoring. Older CNC machines may lack the necessary connectivity, communication protocols, and software compatibility, hindering their ability to operate efficiently within modern production environments. There can be serious consequences as a result of this, including reduced productivity, lower-quality products, and missed opportunities for growth and expansion. Additionally, you may find your operators spending an excessive amount of time working around the capabilities the machine lacks.
Problem #3: Difficulties in Obtaining Spare Parts
This is a painful problem for many CNC owners. A significant challenge associated with obsolete CNC controls is the difficulty in obtaining spare parts. Replacing the same old control with an old control or old spare parts is a disaster waiting to happen. As older controls become less common, it can be the ultimate challenge to find replacement parts when they are needed. Some wil follow the treacherous path of uncertainty by searching eBay for the part they need. Playing a high-risk guessing game without a guarantee it will work when it arrives or if you will find the right one in the first place. If you do find the part, waiting for them to be shipped and arrive to your facility can take a long time resulting in extended downtime and lost profits.
Problem #4: Inefficiency and Inaccuracy
Obsolete CNC controls become less precise and less efficient over time leading to lower-quality products and increased waste. Every miscut costs your company lost profits, increased production costs, and reduced productivity. This can take a toll on your operations and hardworking employees. Can you imagine coming to work and having your highly skilled team do the same job over and over just to get it right because the CNC machine is outdated?
Problem #5: Challenges in Training New Operators
Finally, obsolete CNC controls can make it difficult to train new operators. In today’s world, it can be challenging to find qualified CNC operators who know how to use the machines effectively. If your machine is older or even really old and still running off of floppy disks and black-and-white screens, it may be time to consider how to move forward with the next generation of operators. Having a system that is hard to teach can lead to increased training costs, longer onboarding times, and reduced productivity.
The #1 Solution: Upgrading Your CNC Controls
We understand the perils that lurk with obsolete CNC controls. These top 5 common problems experienced by many CNC owners end up hurting their businesses and their production processes in the long run. Fortunately, there is a reliable solution to keep the machines you have going for years to come. With a CNC controls retrofit, you can solve these problems by upgrading to modern, reliable, and supported controls and eliminate these common problems once and for all.
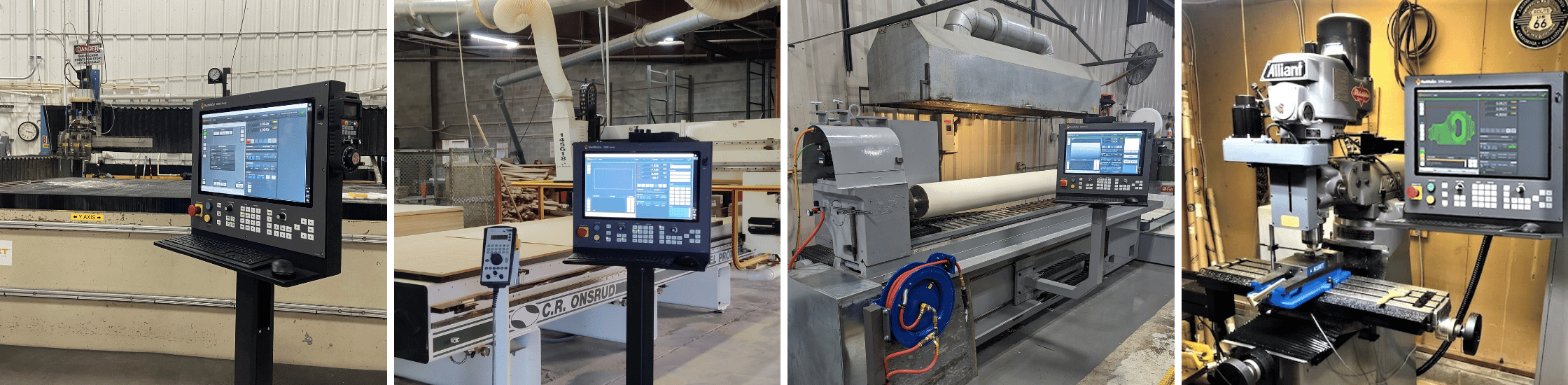
MachMotion offers supported CNC control packages that enable companies to reduce the risks of extended downtime and lost profits. These packages include a new HMI controller with a 21” touchscreen, new Yaskawa motors, a new electrical panel, new cabling, and a wireless pendant to allow you to control the machine away from the controller. With CNC controller retrofits, companies are able to remain competitive and in production while utilizing modern technology. Optimizing your CNC machines gives your team the confidence to continue production without unexpected disruption.