03 Aug LUCAS BORING MILL
LUCAS BORING MILL

1970 Lucas 548 Horizontal Boring Mill Retrofit – HBM
A $56 billion-dollar Steel Company was having trouble with their mill and frequent downtime. The machine was a manual 1970 Lucas boring mill that was previously retrofitted in the 80’s with an Allen-Bradley MP CNC controller. The Lucas boring mill was used as a maintenance machine for the steel plant to make or refinish parts for the production line. Due to the age of the CNC control system, replacement parts to keep the machine running were no longer available. The Steel Company needed a new retrofit solution.
The Problem before
The old Allen-Bradley 8400 MP had become unreliable, causing a tremendous amount of downtime and repair costs. The steel company found themselves spending money to outsource their parts. The company quickly decided to save money by retrofitting their Lucas boring machine. The company’s maintenance contractor first investigated doing the retrofit themselves but as they did more research, they realized they needed to find a company they could partner with. The Contractor searched for a retrofit solution and found MachMotion.
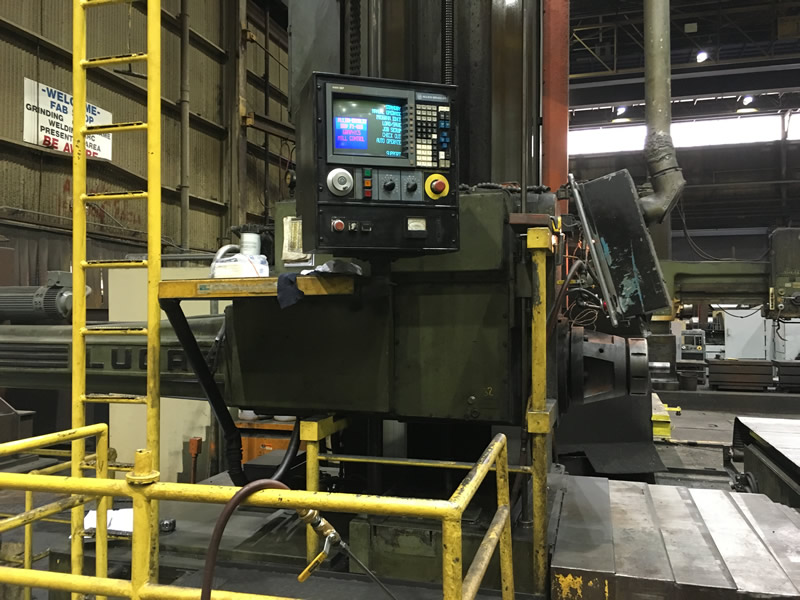
The Solution
Matt at MachMotion was contacted by the maintenance contractor to retrofit their Lucas Boring mill. The maintenance contractor sent pictures of the machine and all the motor tags on the machine. Within a few days Matt was able to generate a final quote for the entire retrofit including the appropriate servos sizes, Allen-Bradley PLC, pre-wired main electrical back panel, control system, power up and commissioning of the full retrofit.
The Contractor wanted confidence that MachMotion quoted the correct retrofit package, as this was the contractor’s first time working with MachMotion. They asked MachMotion to come on site to review the retrofit quote with the contractor and Steel Company to give them the confidence needed to send a P.O. Shortly after, MachMotion received a P.O. and got to work. The Contractor and Steel Company appreciated Matt’s focus on their solution, where other companies had had tried to up-sell to them.
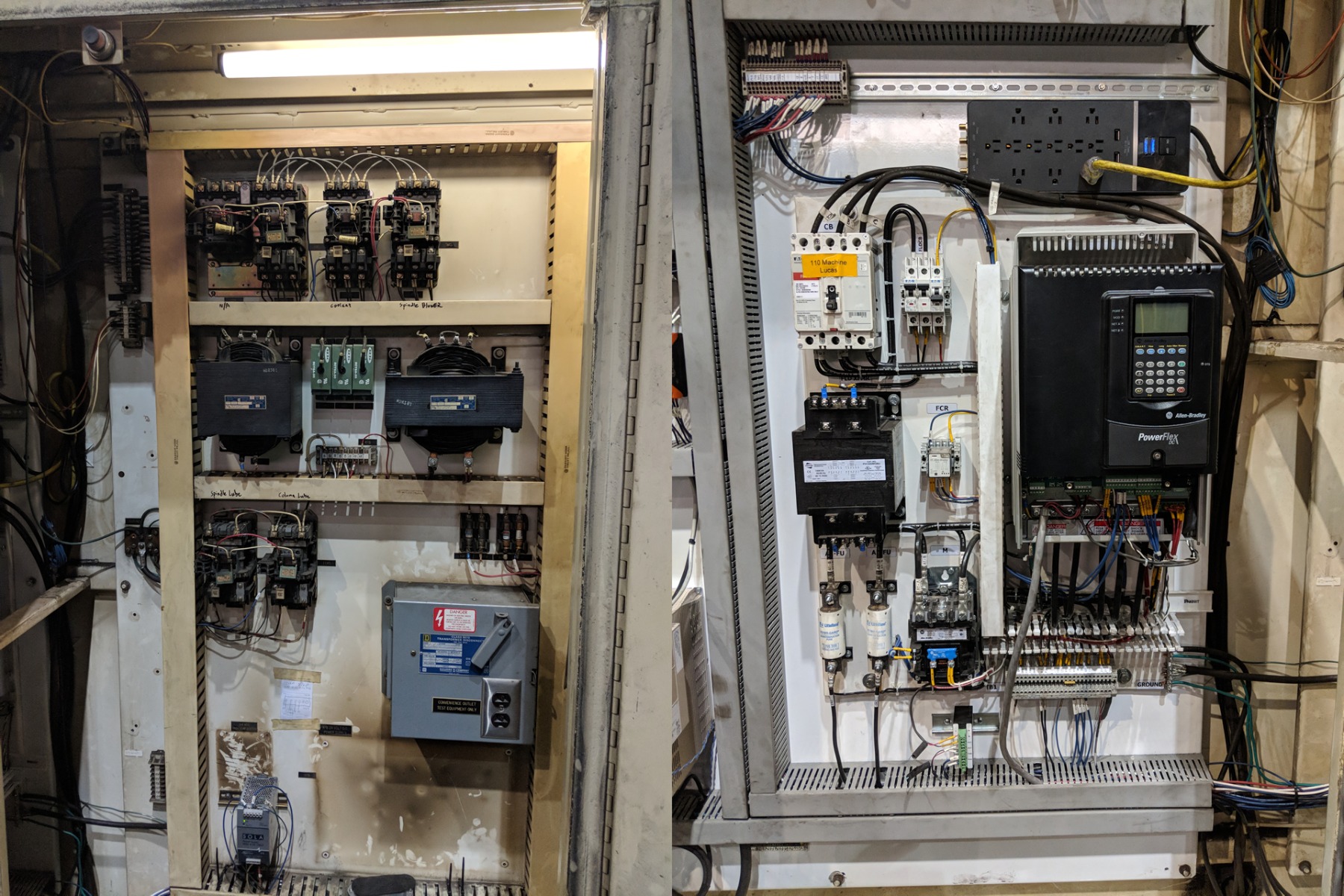
The Results
The new control retrofit installation was a joint effort between MachMotion and the contractor. MachMotion went onsite to the steel company’s facility and did power up and commissioning in one week. MachMotion then returned for onsite training of both the software and operation of the machine. The Steel Company needed the ability to walk up to the machine with a blueprint/part drawing and enter the part dimensional info into the controller and generate the tool path. With MachMotion Alexsys conversational assistant they can program the Boring Mill toolpath at the machine with ease and speed, saving valuable time.
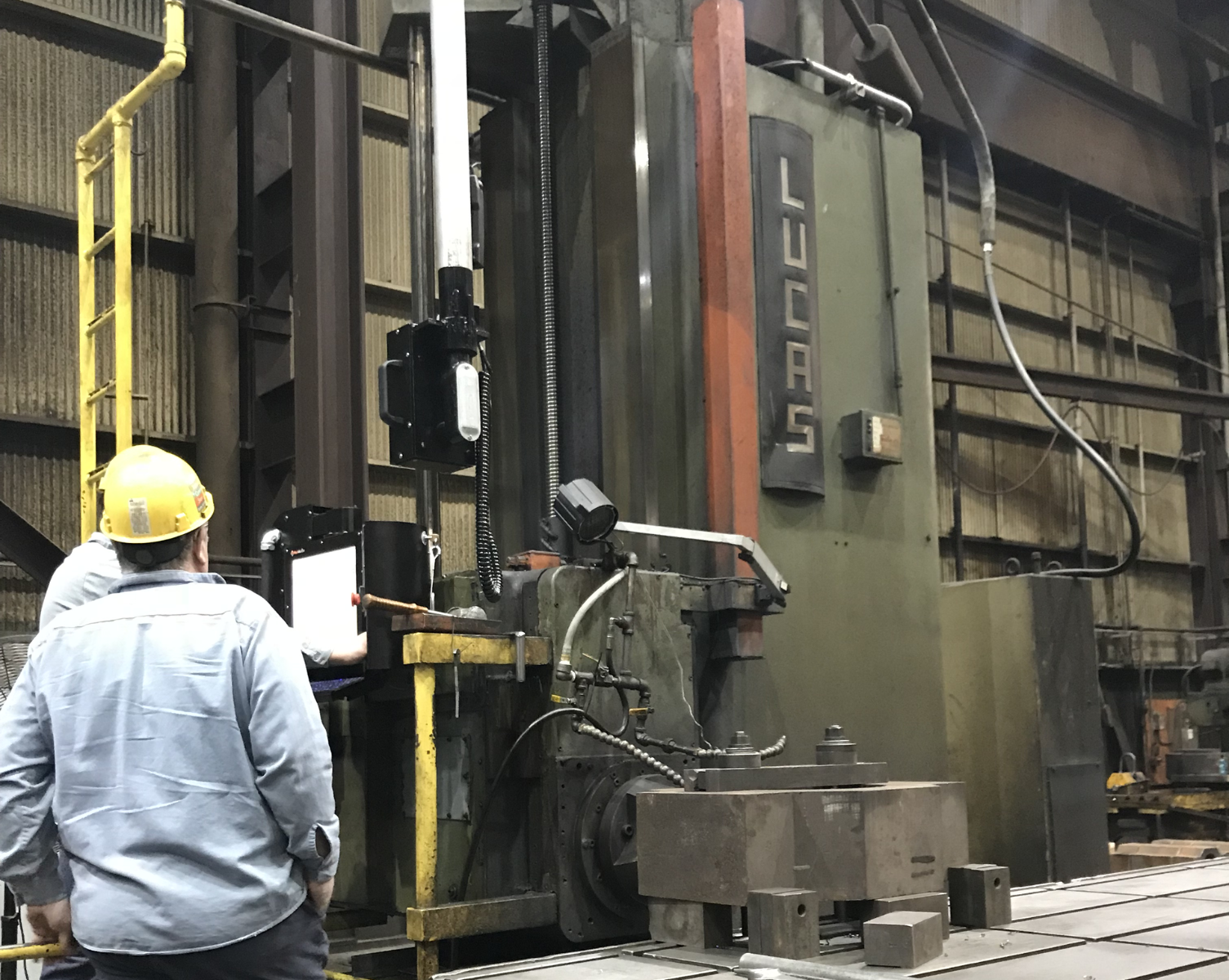
The Conclusion
The Steel Company was very satisfied with their new tools and software. The company was additionally surprised to find out that MachMotion also includes free lifetime support. The Alexsys conversational programming software proved to be an important part of the retrofit and has saved the company time and money. Downtime has become a thing of the past for the Steel Company. MachMotion has made a new partner and written another success story by providing their customers with the highest quality, at a great price.
