30 Sep Extend The Life Of Your CNC Machine: Upgrade, Don’t Replace
Extend The Life Of Your CNC Machine: Upgrade, Don’t Replace
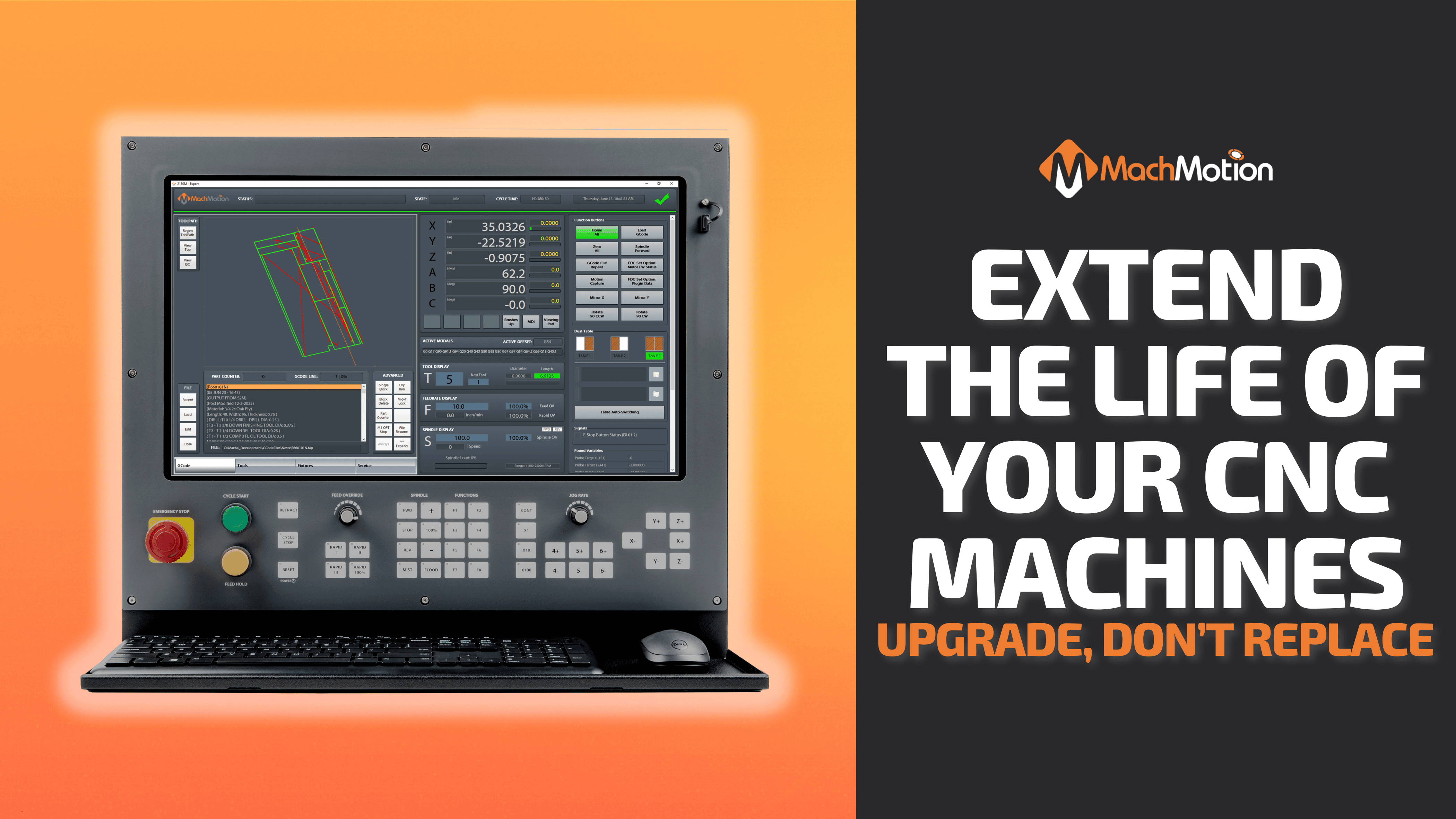
The cost-effective alternative to replacing CNC machines
What does it mean to extend the life of your industrial CNC machine? When your CNC machines start to show signs of aging, it typically starts with the controller. Oftentimes buttons stop working, screens flicker or go dark, and reboots become a necessary task to get the machine to run. Too often, owners only then begin to consider how to solve the problem by gravitating towards replacing the machine with a newer model. After all, newer machines promise advanced features and greater reliability, right? But what if there’s a smarter, more cost-effective way to extend the life of your CNC machine before a complete breakdown—one that allows you to capitalize on the solid iron frame of your existing workhorse while enjoying all the benefits of a new machine?
There is, and at MachMotion, we are all about maximizing the value of your current investment by upgrading the controls rather than replacing the whole machine. Here’s why upgrading your industrial CNC machine can double the life of your machinery and enhance efficiency without the hefty price tag of a new machine.
The High Cost of Replacing CNC Machines
Purchasing a new CNC machine isn’t just a financial burden; it’s a significant operational disruption. Costs can easily exceed hundreds of thousands of dollars when you factor in not only the price of the machine but also the hidden costs like lost production time, operator training, and changes to your existing facility layout. When a new machine arrives, it often requires adjustments to your existing setup, new tooling, and sometimes even new software—resulting in added expenses and extended downtime.
Unlocking the Hidden Value: The Benefits of Upgrading Your CNC
Extending the life of your CNC machines by upgrading the controls can offer similar benefits to buying a replacement system. An upgrade brings the best of both worlds together—modern technology and familiar equipment. This approach will not only extend the life of your machine, but bring additional value to the machine you already know and trust.
Upgrading your CNC machine with MachMotion offers several immediate benefits:
- Cost Savings: Our CNC system upgrades are typically about half the cost of purchasing a new machine. You get to keep your existing equipment while integrating the latest control technologies, ensuring your machine is ready to meet modern production needs.
- Minimal Disruption: Unlike replacing a machine, which can involve weeks or even months of downtime, upgrading with MachMotion can have you up and running in just one week. This keeps your team in production and minimizes lost revenue.
- No CAD/CAM Software Changes: When you upgrade with MachMotion, there are no changes needed to your CAD/CAM software. You can continue to operate with the same systems and processes that your operators are already familiar with.
- Easy-To-Use & Learn: Our CNC system upgrades come with complete operator training in under two hours. This means your team can quickly adapt to the new controls and get back to production without wasting time on extensive training.
- Run Existing Program Files: You won’t have to worry about re-writing a whole library of programs or dealing with post-processor changes. Your existing program files will run without any modifications, keeping your production process smooth and hassle-free.
- Enhanced Security: Upgrading your machine’s control system means up-to-date machine network security, protecting your valuable data from cyber threats.
- Sustainability: Every new machine manufactured has an environmental footprint—raw materials extraction, energy consumption in production, and transportation emissions all add up. By extending the life of your existing CNC machine, you’re making a choice that’s not only good for your bottom line but also for the environment.

Don’t Wait for a Problem With Your CNC Machine – Make A Plan
Having a plan means you’re prepared, protected, and positioned for continued success. Making a plan before CNC controller problems arise is essential to minimizing costly downtime, avoiding expensive repairs, and maintaining production. Proactive planning to increase your CNC machine’s lifespan allows for timely maintenance and upgrades, preserving machine value and operational efficiency. It also reduces stress on you and your team while ensuring you remain up and running by avoiding unexpected disruptions.
Why MachMotion Is the Right Partner for Your CNC Controller Upgrade
With decades of experience in extending CNC machine life through strategic upgrades, MachMotion has helped thousands of businesses breathe new life into their machines. Our approach is not just about retrofitting hardware; it’s about transforming your equipment into a more reliable, efficient, and productive asset. We eliminate the guesswork and risks involved in purchasing used machines. You avoid the potential pitfalls like unknown wear and tear, lack of historical maintenance records, and compatibility issues. When you extend the life of your CNC machine with MachMotion, you get a machine that’s production-ready and fully supported by a team that understands your needs. Visit our social media like our Facebook or YouTube to see examples of our customer’s success!
Extend The Life Of Your CNC Machine With Confidence
Upgrading your CNC machine is a strategic investment that pays dividends in both the short and long term. With MachMotion, you get a solution that’s tailored to your unique needs, backed by industry-leading expertise and support. Don’t let unplanned downtime dictate your production schedule or your bottom line. Make the smart choice and explore how upgrading can extend your CNC machine life and keep your operations running smoothly for years to come. To learn more about CNC controller upgrades, click here.
Another way CNC owners are losing money with their machines is through the learning curve and inefficient machining. Outdated CNC controls are not only hard to learn how to operate, but they also can’t keep up with the demands of modern machining. This results in slower onboarding of new operators and less accurate operations. This can also lead to wasted materials from mistakes being made, longer machining times, and increased training time, all of which can cost CNC owners a significant amount of money.
With a CNC retrofit, you can upgrade your machine’s control system to a new system that is easy-to-learn and efficient to run. This means faster onboarding and more accurate operations, which can reduce scrap rates, save on time & materials, and ultimately increase profitability.